The Problem
The Solution
Statistics
Symptoms
Technique
Equipment
AOPA Article
A Balancing Tour
Gallery
Vibration Analysis
Links
| |

If you have a vibration problem that is not due to prop
unbalance, a
recording and reading of the spectrum analysis (a little like reading tea
leaves) may help sort things out. Since the Harmony analysis methodology is a proprietary way of proceeding along these lines I would be loathe to disclose
all of the specific details of it online. Please feel free to
contact me with the specifics of your problem and I will do my best to assist
you. The following short course
in aircraft vibration covers only a few of the angles and issues I consider
during a custom designed comprehensive analysis. Still, it is a decent primer
whether you can work directly with me or not.
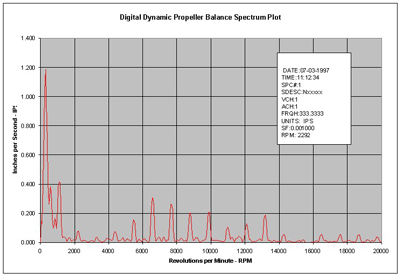
Engine
vibration analysis is a difficult science as spectrums (engine signatures)
are all unique. Not all the peaks are always seen, nor are the amplitudes
the same for every engine, even of the same type and model. The "signature"
is as unique as an individual. Two people named Anne Smith don't sign their
names the same, nor are they the same, even though we might be able to read
both names as the same name. We know enough about the first order that we
can either fix it by balancing, or instrument the prop enough to tell if
it's a crank problem or a prop problem. How common is balance a problem?
About 90% of the time an improvement can be
made. Of that 90% there is a standard bell curve distribution, with the
center of the bell around .4 IPS. A small number will be just above .15 IPS,
the generally accepted limit, and a few will be quite high, around .8 and .9
IPS, but most fall in the .2 to .5 IPS range. For the layman, .5 IPS at 2000
RPM equals about .005 inch radial runout on the crank flange. Point 2 IPS
(0.2) equals .002 inch and it's best to get that down to .05 IPS; .0005 inch
radial runout 10r a really smooth balance. That's considerably less than the
clearance in the front main journal bearing, so now you are running on oil,
and not working the oil too hard. To you purists, again, you are running on
the oil at .005 inch but you are depending on the oil to cushion the crank,
which wears out the oil faster and makes it run hotter. If the propeller is
over 1.2 IPS, you are probably scraping the babbit of the bearing a bit. We
draw the line at 1.2 IPS as a balance candidate. This puts the vibration
correction in the mechanical fix action slot. It is probably not a routine
balance problem. It could be anything from a poor static balance to a broken
crankshaft. It's not worth finding out in the air!
MOTOR MOUNTS
The half order is probably the most commonly griped vibration, Sadly, it is
also one of the most difficult to diagnose and reduce. The motor mounts need
to be very soft to attenuate this low frequency vibration. This has two
undesirable side effects in aircraft applications. The engine moves more on
the mounts so clearances to allow for abrupt landings and gust loads must be
greater. The other unfortunate side effect is that soft mounts do not
attenuate high frequency vibration very well. This is very bad for gyros and
sensitive electronic gear. The amount of 1/2 order vibration in a given
engine varies engine to engine of the same type. Typical ranges might be .2
IPS for a very good engine and up to .8 or .9 IPS on an engine that is
otherwise healthy in every respect. Fixing a problem case has three areas of
concern. How bad is it on the engine (the forcing function), how well is it
being attenuated (damping). and is there anything that is naturally
resonant. A typical upper class balance job will include a spectrum
analysis. This will at least identify the levels found on the engine.
The next task is to determine what the levels in the cabin are to find out
if it is a transmission problem. If the levels in the cabin are more than
those found on the engine it is likely a resonance problem. If they are the
same or less but still objectionable, the only recourse is to visually
inspect the mounting system (isolators and engine mount) as well as look for
hard contact areas in the engine compartment.
I saw one STC'd engine installation that
used rubber mounts for the engine but hard mounted the exhaust system to a
turbo which was hard mounted to the firewall. This constituted a "hard link"
from the engine to the airframe. The engine ½ order was very obvious in the
cabin.
About engine isolators/mounts...
Here's a brief primer on how mounts attenuate vibration. The mount is for
all practical purposes a spring. What this spring does is absorb vibration
by internal resistance to oscillating. As the spring oscillates it absorbs
energy. Because of resistance it heats up as it absorbs energy. Spring steel
has very little internal resistance and is usually accompanied by an
"absorber" which increases its' resistance. The spring rate (constant) of
the mount is derived by (1) the frequencies of interest, (2) the amplitudes
expected (capacity), and (3) the weight they need to support. Most aircraft
use elastomers (compounds of elastic material) that have a spring
rate appropriate to engine frequencies.
The dilemma is in choosing one that
satisfies all the frequencies produced by the engine. Usually, the
elastomers are only good in a narrow range of frequencies. Since high
frequency vibration (lots of cycles) are the most damaging, it is logical to
treat the higher frequencies as the more important to attenuate.
Unfortunately, a mount that damps high frequency makes a poor mount for low
frequencies. What we end up with in the airplane is a mount that damps the
high frequency vibration produced directly by the engine, while the lower
frequency 1/2 order vibration is passed with less restraint. There are some
mounts that actually amplify the 1/2 order! On the higher frequency side,
the buzz most people feel in the cabin cannot be attenuated since it is a
function of the aerodynamic pulsing of the propeller on the windscreen and
empennage (single engine) or sides of the fuselage (twin). This is acoustic
energy converted back to mechanical energy. Some twins have tuning forks in
the side wall of the aircraft to absorb (cancel) this vibration and they are
quite effective.
I'm going to depart for just a minute to cover a bit of entomology (bug
science) to illustrate how tuning forks work. The crane fly (some people
call it a daddy long legs) is an air craft of sorts. It has long wings and
lots of dangly appendages. This plan form is fraught with possibilities for
resonance in flight but the crane fly has two small appendages immediately
behind and below the wings with small masses at the ends. When viewed under
a stroboscope so they are viewed in slow motion, the pendulous dampers can
be seen to flex in opposition to the wings. This is the way the crane fly
damps vibration. Well, if it's good enough for mother nature, it must be
good enough for an airplane which is far less complex. The only problem with
tuning forks and pendulous dampers is they are generally only good in their
"tuned" region. Both mass and spring rate control tuned region. The rule
being, the heavier and less resilient, the lower the frequency, and the
lighter and stiffer, the higher the natural frequency. The mount depends on
its internal resistance to tune it to the desired frequency. This resistance
can and will change in operation due to prolonged exposure to heat (bakes
and hardens them) and solvents like oil, fuel, and cleaning solvents (breaks
them down and softens them). Both conditions are bad. A hard mount is more
likely to put more stress on the engine tubular or sheet metal mount
structure because the high frequency (hence more cycles) is passed. A soft
one could allow the engine to sag, enough for the prop to hit the cowling
during hard bounces. Further, the mount elastomers are sometimes "tuned" by
placing one spring rate on the top and one on the bottom, or by placing
elastomers of different rates at different positions on the engine.
Failure to adhere to these installation schemes is VERY detrimental to
the purpose of the mount! As far as items mounted on the engine mount tubing
itself this is a mixed bag. It is possible to "tune" the mount to an engine
peak by changing the weight of the mount. Each leg of the mount has a
different resonance, even among mounts of the same part number. By adding
weight to a leg or legs, the natural frequency is of course changed. Usually
it's not a problem. When in doubt, make it as much like it came from the
factory, or as much like a factory installation as you can.
Allow me to diverge. Geared engines are
problematic in that now we have two rotating masses with their associated
harmonics. What do you suppose happens when an engine is running at 4000 RPM
and the two bladed prop only turns 2000 RPM. Well, you've got propeller one
per rev talking to engine half order, and you've got propeller twice order
(aerodynamic) talking to the crankshaft. This is a recipe for some very
annoying airframe vibrations and one reason most production gear ratios are
set up in primes or fractional thirds. The prop might turn .66 time the
engine,. In this manner none of the natural peaks of one can influence the
natural frequencies of the other. Home builders should take not here. If you
are designing a gear reducing unit, say at least 10% away from a half or
whole number of the engine RPM. Do not run the engine 1.5, 2.0, 2.5 etc.
times the prop speed. Pick an odd and even number of mating teeth or cogs
for the driving and driven gears and adequate harmonic separation will
eliminate most of these problems.
CABIN MEASUREMENTS
As there are no accepted norms for readings taken in the cabin, whatever you
get is subject to some interpretation. In the helicopter world vibration
"footprints” are quite common, in the fixed wing world almost non existent.
In any event, frequency will determine what it is.
With a baseline signature the very least
you will do is be able to track improvement or deterioration when changes
are made. Some people inadvertently hurt themselves. On numerous occasions I
have been called on to take readings on a new engine that vibrates more than
the old one did. Turns out that, since the airplane would be down for a
while the owner decided to revamp the instrument panel too. When the weight
of the panel was changed, the natural resonance of the panel changed too,
causing what honestly appeared to be a "bad" engine. Taking a measurement on
another airplane of the same type, similarly configured (same engine, same
prop) is very valuable in generating a known good sample. Reproduce the
running condition as exactly as possible and compare. Since this is not an
option on most antiques and difficult on a lot of classic aircraft, it's a
good idea to have a signature run when it is running well, or at least
before you do anything drastic like replace the engine. This will give you
an adequate baseline from which to compare.
A word about props...
Propellers are simple devices but they are one of the most neglected parts
of the airplane. Nearly everyone checks the prop and spinner on the
preflight but there are some things you just cannot see. As an airplane
descends from altitude, air will find its way into every crack, crevice and
hole as the atmospheric pressure increases. The air in the lower altitudes
contains a good deal more moisture than at altitude so what you get is an
automatic injection of water. This water accumulation is cumulative. Most
airplanes are parked shortly after the descent and this moisture can
condense out on cool metal surfaces at night. On propellers, the cavity
inside the blade makes a good place for this. This condensate sits in the
root of the propeller, or can find its way on the surfaces of steel parts
and cause a good deal of corrosion. Corrosion on propeller parts is very
bad. In the propeller root it can and has caused separation of the blade
from the hub, usually followed shortly after by the engine. Devastating is
the word. Some propeller manufacturers specify a calendar overhaul period. I
read in a lot of the aviation journalism that this is a negative for a
potential airplane owner. Not really. It shows a great deal of prudence on
the part of the propeller manufacturer in maintaining a customer base (by
keeping them alive) and lowering everyone's liability bill. In speaking with
a propeller shop owner the other day he said he received a controllable
pitch propeller that had not seen an overhaul since 1961! The propeller had
so many AD's against it almost cost as much for the AD compliance as a new
prop. This was neither responsible maintenance or ownership. This was a
gamble.
Some of the signature peaks are easily correctable, others are not. What are
the big hitters?
Engine half order -Vibration produced at half engine speed
Engine first order -Vibration produced at prop speed or crank speed Engine
second order- Vibration produced at twice engine speed Propeller- Vibration
produced at the prop speed "N" per rev Other -Accessories at ratios other
than whole numbers or half numbers. Upper order harmonics - for this
discussion higher than first order but a ratio of half plus a number, or
even or odd numbers times the crank speed.
ENGINE HALF ORDER:
Half order vibration is probably the most
complained about vibration in any piston installation. Remember every other
stroke there is a power stroke? This is relatively low frequency vibration.
One of the characteristics of low frequency anything is it doesn't take much
energy to travel very far. Think about radio waves. Low frequency travels
very well on very little power, the reason HF radios are used for long range
communication on mobile platforms or where there isn't much power available.
To move high frequency radio waves takes energy. Like radio waves, the half
order travels well, and despite the best intentions of the manufacturers the
isolation mounts on the engine may not substantially reduce the half order
levels. In some aircraft they are actually amplified. This is usually felt
as a drumming on the floorboards, or shake in the yoke or glareshield. If
your ashtray is rattling, it's either the prop out of balance or the 1/2
order Vibration!
The following affect the half order vibration:
Anything that controls the combustion cycle on the engine is pretty wide
territory for troubleshooting. It could be compression, mixture, induction
losses. valve lift, spark timing, or anything that controls the combustion
cycle in the engine! Turbocharged engines seem to suffer with this malady
regularly due to the lower compression ratios and higher horsepower output.
Interestingly, some of the crop of "blueprinted" engines, engines whose
parts are held to more stringent tolerances typically exhibit low half order
levels. In fact, they exhibit lower vibration levels throughout their
spectrum. Less vibration, smoother flow, more horsepower. Does this mean we
should all have blueprinted engines? Buy what you can afford. But be sure
you can afford what you buy!
ENGINE FIRST ORDER
Propeller balance and propeller track affect the first order vibration.
Remember first order vibration occurs for each revolution of the engine in a
direct drive engine. On the surface it seems easy to just balance the
propeller and be done with it, but there is more to it than that for a
couple reasons. One, it is not just the balance of the propeller we are
concerned with, but that of the crankshaft as well. In a routine
balance exercise when the propeller is out of balance, the rear of the
engine vibrates out of phase with the front. The center of the rotation is
the nodal point where there is little vibration. For this reason, the center
of the engine is a poor location for balance. Anyway, as the propeller is
balanced, the rear of the engine also decreases in amount until the whole
crank is running on a true line. If the sensor mounted at the front of the
engine reads low but a sensor placed at the rear of the engine remains high or
goes higher, the propeller mass balance is not the problem. It is either an
out of balance of the crankshaft or out of track (thrust distribution
inequality) of the propeller. As I have developed a keen sensitivity for the
wing tip vibration 'feel', I normally only install a second accelerometer
when I 'feel' the vibration hasn't improved after DPB-- even though
the vibe level at the front mounted accelerometer is reading near zero.
ENGINE TWICE ORDER:
Engine twice order has as an origin two sources. If the engine has a two
blade propeller, obviously the two pulses per rev as the accelerated air
will be evident. The other source is reciprocating mass imbalance. That
means the reciprocating masses (pistons and rods) are not canceling each
other. Here again, on a "blueprinted" motor, the 2nd orders are generally
very low. When top end work is done helter skelter, with no attention to
piston size or weight, the engine just will not run as smooth.
OTHER SOURCES
Ignoring the core engine vibration produced for a moment, there are
accessories that can create problems, and lets not overlook the airframe.
The alternator on most recips is belt or gear driven at some other frequency
around 3 to 5 times the crank speed. Since it is not an exact multiple. its
pretty easy to pick out in the spectral plot. This is true of air
conditioning compressors, pumps and other accessories on the engine. To
determine the exact speed of the accessory drive pad. just look at the
accessory drive train ratios in the overhaul manual and multiply them by the
engine RPM.
Air frame vibrations are as difficult to
track down. They're usually airspeed or angle of attack sensitive. By hand
holding the velocimeter sensor inside the cabin, and comparing this plot to
the engine signature the engine generated, points can be subtracted form the
airframe and yield a starting point. Some strange things can be found, from
noisy bearings in a gyro, to wheels that spin in the wells, to weather
stripping that vibrates.
To balance the prop a velocimeter (also known as an accelerometer) is mounted securely on the engine case
where it will measure vibration. The photocell is mounted where it will time
a small retro-reflective target on the back of a propeller blade. This
provides a timing pulse so the vibration orders can be set up in the
instrument. A lead is run from the sensors to the vibration computer and the engine is ready to run. The signature is taken at some run
condition, say 2100 RPM, and flat pitch on the propeller. The process of
acquiring a reading takes about 15 to 30 seconds. The black box measure
vibration signatures via a 400 bin Fast Fourier Transform. Dr. Fourier
reasoned that any complex signal, like a vibration signature, could be taken
apart into its constituent parts and represented as individual amplitudes
(amount) and frequencies (speed). To do this the signal must be sampled, and
then reproduced in some x/y format. Remember the bell earlier? It didn't
have just one frequency when it was struck. If it did it would sound no
different than an electronic beep from a computer speaker. It consisted of
many frequencies and different amplitudes. If it were represented as a
spectrum, we could see by looking at the frequencies, many if not most are
harmonically related. The same is true of an engine. Most items are
harmonically related to the crankshaft. So what are they and what do they
mean?
Lets look at a typical four banger flat opposed motor signature. It has a
peak at 1/2 order, some at first order (the crank speed), some at 1.5. 2.0,
2.5, 3.0 etc. Since these are ratios of the crankshaft speed, we will see
peaks at 1000 RPM intervals for an engine running at 2000 RPM. Generally
these diminish at the higher frequencies over about 5th order - five time
the engine speed.
Thrust inequalities are more pronounced in changes with pitch so a simple
change in load on the prop will identify this quickly enough. If the point
remains the same over pitch, by a process of elimination, the only problem
left is residual out of balance of the crankshaft. It is either out of
balance or bent. To check for a bent crank, change the prop orientation on
the crank 180 degrees. If the phase angle of the imbalance changes 180
degrees, it's the crank, not the propeller, because the crank is showing up
at the same place relative to the imbalance. Before blaming this expensive
piece of machinery though make one last check. This is assuming you've
already checked the static track of the propeller.
Conclusions
Have your propeller balanced. Its well
worth the cost and effort.. The challenge here is finding an experienced
balancer. I don’t expect you’ll find someone in your are with my experience
(25 years of full time balancing, ~500,000 car miles and over 6500 balanced)
Since he/she is getting paid to learn, an
amateur (any A&P who has balanced less than ~250 props, this includes all
but three balancers I know of in the country) should be compensated
appropriately. He should not have to pull any case bolts to attach the
accelerometers. He should know how to quickly hot start your engine and
should need no more than 3 engine runs and 2 hours to get the job done,
de-cowl, setup to log entry. If he drills holes to install permanent weights they
should be micro-countersunk, reamed and de-burred. Weight amounts should be
converted to inside radius after balance. These are about half of my main
concerns, however, if your balancer can address these, he's probably OK.
While interviewing a tech I'm
not sure you could ask all the questions to satisfy my concerns without
causing some irritation. If you find a balancer with at least a few testimonials or referrals I would just give him the airplane and
keep your fingers crossed.
Equipment type is only a minor
concern. The main differences between boxes is in the operator interface structure used. The
manufacturers provide a minimum of instruction to keep costs down (usually a
video) and market prop balancing as a "No Brainer" in order to sell as many
units as possible and compete for a very limited market. Typically the
equipment is fairly easy to master, the devil is in the myriad practical
details involved in executing a truly precise balance on a complex
reciprocating powerplant.
Finally--Maintain the integrity of the
engine mounts with periodic replacement. The rubbers get cooked, bathed in
oil and frozen. They deteriorate in ways you cannot see. Operate the engine
smoothly. Use a reputable engine overhauler when the time comes.
|